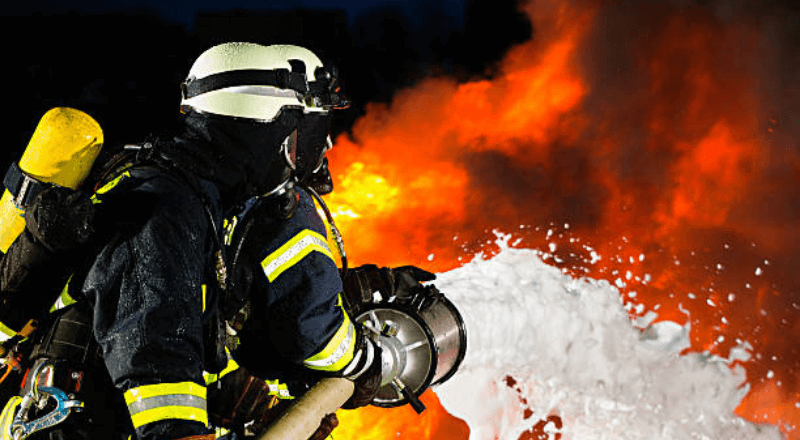
Fire fighting using foam: The three most important things to consider
Class B fires are those which involve flammable liquids, liquefiable solids, oils, greases, tars, oil-based paints and lacquers (i.e. flammable and combustible liquids). Combustion of these occurs entirely in the vapour phase that is present above the surface of the liquid.
Class B fire cannot be extinguished by water as it is generally much denser than liquid hydrocarbons; consequently, when applied during fire fighting, it immediately sinks below their surfaces without having any beneficial effect. In fire fighting terms, the application of water may cause the surface area of the fire to increase and spread to previously unaffected areas. Hence Foam is the preferred choice for Class B fires as it provides a visible blanket that controls and extinguishes these fires faster and more effectively than water.
However, the efficient use of foam during fire fighting depends on 3 important factors which are the foam expansion ratio, selection of foam equipment and the suitable foam chemical used. Let us understand in detail how each of these factors contribute to success
I) Foam Expansion Ratio
The finished foam is usually classified into three types ie low, medium or high expansion. The expansion ratio of foam is the ratio of the volume of the finished foam to the volume of the foam solution used to produce it.
- Low expansion: ratio less than or equal to 20: I
- Medium expansion: ratio greater than 20: I but less than or equal to 200: I
- High expansion: ratio greater than 200: I
Commonly expected fire scenarios and the foam expansion ratio desirable for fire fighting are as below
Low expansion (LX)
- Large flammable liquid fires (i.e. storage tanks, tank bunds)
- Road traffic accidents
- Flammable liquid spill fires
- Vapour suppression
- Helidecks
- Jetties
- Aircraft crash rescue
Medium expansion (MX)
- Vapour suppression
- Flammable liquid storage tank bunds
- Small cable ducts
- Small fires involving flammable liquids,
- Transformer fires
High expansion (HX)
- Protection of, large volumes such as warehouses, aircraft hangars, cellars, ships holds, mine shafts, etc.
- Large cable ducts
- Vapour suppression (including cryogenic liquids such as LNG/LPG)
Hence understanding the foam expansion ratio required for each scenario is the primary step in planning your response
II) Selection of Foam Equipment
It is important to note that these above-mentioned foam expansion ratios can be obtained only by using purpose-designed foam-making branches or mechanical foam generators.
Using a conventional nozzle such as short branch, fog nozzle, or water spray nozzle, can only produce expansion ratio up to 4:1 and will lead to poor foam quality, due to insufficient agitation of the foam/air mixture. That means the foam produced from these types of equipments will have a very low expansion ratio and a very short drainage time.
So if you are using foam, make sure you have a foam branch attached to your delivery hose. Nowadays foam attachments are supplied with all kinds of modern fire fighting nozzles commonly referred to as “Foam Tips” which can be used for foam generation.
Following Foam-making equipments are generally used for producing finished foam
- LX hand-held foam-making branches;
- LX hand-held hose reel foam unit;
- LX foam generators;
- LX foam monitors;
- MX hand-held foam-making branches;
- LX and MX hand-held water branch ‘snap-on’ attachments;
- MX foam pourers:
- HX foam generators
LX Foam Branch MX Foam Branch HX Foam Generator
Depending upon the foam expansion required, suitable foam-making equipment needs to be used.
III) Suitability of Foam Chemical
There is a misconception that the same type of foam chemical can be used for producing all types of foam. However the quality of finished foam depends on the type of foam concentrate as well. Commonly available foam concentrates and their applications are given below
Protein Foam:
Protein foam concentrates are inexpensive and are usually manufactured for use at 3% or 6% concentrations. They are only intended for the production of low expansion finished foam.
Fluoroprotein (FP) Foam:
FP foam concentrates consist of protein foam concentrates with the addition of fluorinated surface-active agents. FP foam concentrates are usually available for use at 3% or 6% concentrations and versions are available for use with sea and freshwater. FP foam concentrates are primarily intended for the production of low expansion foams although they have also proved effective when used to produce medium expansion foam. They are not recommended for the production of high expansion foam.
Film-forming Fluoroprotein (FFFP):
FFFP foam concentrates are based on FP foam concentrates with the addition of film-forming fluorinated surface-active agents. FFFP foam concentrates are usually available for use at 3% or 6% concentrations. They are primarily intended for the production of low expansion foam although they can also be used to produce medium expansion foam. FFFP foam concentrates are not recommended for the production of high expansion foam.
Aqueous Film Forming Foam (AFFF):
AFFF foam concentrates are usually available for use at 1%, 3%, or 6% concentrations and versions are available for use with fresh and seawater. They are primarily intended for the production of low expansion foams although they can also be used to produce medium expansion foams. Due to their film-forming properties, they can be applied secondary aspirated and can be used to tackle class A fires. AFFF foam concentrates are not recommended for the production of high expansion foam.
AFFF is widely accepted for crash rescue fire fighting uses and on less volatile fuels such as kerosene and diesel oil. It is widely used in offshore as secondary aspirated foam for helideck protection at a concentration of 1%
Alcohol Resistant Foam Concentrates (AFFF·AR and FFFP-AR):
Alcohol resistant foam concentrates have been developed to deal with fires involving water-miscible liquids such as alcohols and some petrol blends containing high levels of alcohols. Alcohol resistant foams can also usually be used on hydrocarbon fuels and because of this are sometimes known as multi-purpose foams. Alcohol resistant foam concentrates are normally used at 6% concentration for application to fires of water-miscible fuels, such as most polar solvents, and 3% concentration on liquid hydrocarbon fuel fires.
Synthetic Detergent (SYNDET):
SYNDET foam concentrates were developed from early synthetic detergent foams and are based on a mixture of anionic hydrocarbon surface-active agents, solvents, and foam stabilizers. SYNDET foam concentrates are versatile, as they can be used to produce low, medium, and high expansion foams. SYNDET foam concentrates are usually manufactured for use at between I% and 3% concentrations and versions are available for use with sea and freshwater.
Hazmat Foam Concentrates:
Many chemicals destroy fire fighting foams either by reacting with them or by extracting the water from foam blankets. Hazmat foam concentrates have been designed to be effective on products that destroy foams by chemically reacting with them. Versions of these foam concentrates are available that have been formulated to be resistant to either extreme acidity or extreme alkalinity. They are often used to produce medium expansion foams with optimum expansion ratios of around 60: I.
If there is doubt concerning the suitability of a foam concentrate for a particular task, the manufacturer of the foam concentrate should be consulted to ensure that it can be used safely and successfully.