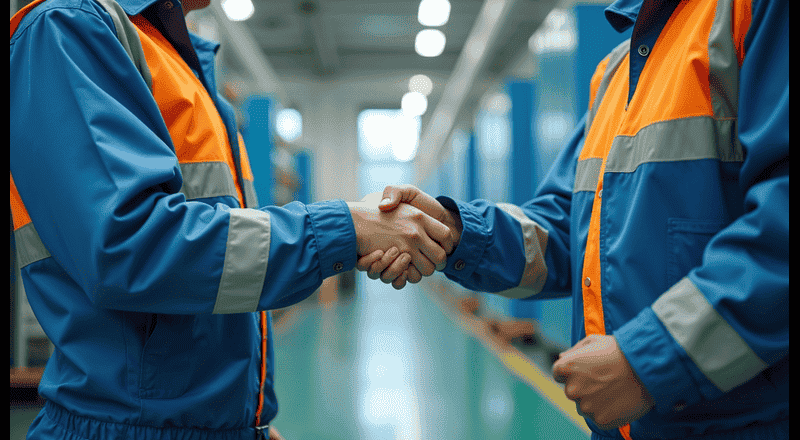
Are You Making These 7 Behaviour Based Safety Mistakes?
Behavior based safety is a powerful approach to reducing workplace incidents, but it’s easy to make critical mistakes that undermine its effectiveness. From overlooking near misses to neglecting employee involvement, these errors can have serious consequences. In this post, we’ll explore seven common behavior based safety mistakes that might be lurking in your organization. By identifying and addressing these issues, you can transform your safety culture and create a more secure work environment for everyone.
Ready to uncover the hidden flaws in your safety program? Let’s dive into the seven crucial mistakes you need to avoid to ensure your behavior-based safety initiatives are truly making a difference.
Overlooking Near Misses
One of the most common mistakes in Behaviour Based Safety (BBS) implementation is failing to report nearmisses and minor incidents. Many employees hesitate to report small accidents or near misses, thinking they’re insignificant. However, these seemingly minor events can be crucial indicators of larger safety issues.
Consider the following statistics:
Incident Type | Frequency | Potential for Learning |
Major Accidents | 1 | High |
Minor Incidents | 10 | Medium |
Near Misses | 30 | High |
This table illustrates the “Safety Triangle” concept, emphasizing the importance of reporting all incidents, no matter how small.
Another critical mistake is ignoring warning signs. These can include:
- Repeated minor incidents in a specific area
- Employees expressing concerns about certain procedures
- Equipment showing signs of wear or malfunction
Ignoring these warning signs can lead to more serious accidents down the line. A robust BBS audit should include a thorough examination of these potential red flags.By overlooking near misses and minor incidents, organizations miss valuable opportunities for prevention. These events can provide insights into:
- Weaknesses in current safety protocols
- Areas where additional training is needed
- Potential equipment or process improvements
Implementing a comprehensive behaviour based safety checklist that includes reporting and analyzing near misses can significantly enhance your safety culture. Remember, every reported incident, no matter how small, is an opportunity to prevent a more serious accident in the future.
2. Inadequate Employee Training
One of the most critical mistakes in behaviour based safety (BBS) is the absence of comprehensive safety programs. A well-rounded safety program should cover all aspects of workplace safety, not just the basics. Here’s why comprehensive programs are essential:
- Holistic approach to safety
- Addresses various risk factors
- Promotes a safety-first culture
Component | Purpose |
Risk assessment | Identify potential hazards |
Safety protocols | Establish standardized procedures |
Emergency response | Prepare for unexpected situations |
Continuous improvement | Regularly update and refine practices |
Safety knowledge and skills can fade over time if not regularly reinforced. Infrequent refresher courses can lead to:
- Outdated safety practices
- Decreased awareness of potential hazards
- Complacency in following safety protocols
To maintain a high level of safety consciousness, organizations should implement regular refresher courses as part of their BBS implementation strategy.
New employees are particularly vulnerable to workplace accidents due to unfamiliarity with the environment and specific job hazards. A comprehensive new employee orientation should include:
- Introduction to company safety culture
- Overview of safety policies and procedures
- Hands-on training for job-specific safety equipment
- Clear communication of reporting procedures for safety concerns
Each role within an organization comes with its unique set of risks. Failing to address these specific job hazards in training programs can leave employees ill-prepared to handle potential dangers. A thorough BBS audit should identify these job-specific risks and ensure that training programs are tailored accordingly.
By addressing these aspects of employee training, organizations can significantly improve their BBS implementation and create a safer work environment. The next crucial step is to ensure that safety policies are effectively communicated throughout the organization.
3. Poor Communication of Safety Policies
When it comes to behavior based safety (BBS), clear and concise safety guidelines are crucial. Ambiguous or poorly defined guidelines can lead to confusion and inconsistent implementation of safety practices. To ensure clarity:
- Use simple, straightforward language
- Provide specific examples and scenarios
- Include visual aids when possible
Here’s a comparison of unclear vs. clear safety guidelines:
Unclear Guideline | Clear Guideline |
“Use proper PPE” | “Wear safety goggles, hard hat, and steel-toed boots in designated areas” |
“Be cautious with machinery” | “Lock out and tag out equipment before maintenance or repairs” |
“Keep work area clean” | “Clear debris from walkways and workstations at the end of each shift” |
Even the best safety policies are useless if they aren’t effectively communicated to employees. Improve information dissemination by:
- Utilizing multiple communication channels (e.g., emails, posters, meetings)
- Regularly reinforcing safety messages
- Translating materials for non-native speakers
- Implementing a safety information management system
Encouraging open communication about safety issues is essential for a successful BBS program. To foster dialogue:
- Establish anonymous reporting systems
- Conduct regular safety meetings and toolbox talks
- Create a non-punitive environment for raising concerns
- Recognize and reward employees who contribute to safety improvements
By addressing these communication challenges, organizations can significantly enhance their BBS implementation and create a more robust safety culture.
4. Inconsistent Enforcement of Safety Rules
Inconsistent enforcement of safety rules can significantly undermine the effectiveness of a Behaviour Based Safety (BBS) program. One common mistake is selective rule application, where certain safety rules are enforced more strictly than others. This inconsistency can lead to confusion and resentment among employees, ultimately compromising the overall safety culture.
Consider the following examples of selective rule application:
- Enforcing PPE use in some areas but not others
- Strictly monitoring speed limits for some vehicles but not all
- Applying safety protocols differently for different shifts or departments
To avoid this mistake, organizations should:
- Develop clear, standardized safety protocols
- Communicate expectations consistently across all levels
- Regularly audit compliance in all areas
- Address discrepancies promptly and fairly
Leadership plays a crucial role in the success of any BBS implementation. When managers and supervisors fail to follow safety rules themselves, it sends a powerful negative message to the workforce. This hypocrisy can erode trust and undermine the entire safety program.
Leadership Behavior | Impact on Safety Culture |
Following all rules | Positive reinforcement |
Occasional lapses | Mixed messages |
Frequent violations | Undermines safety efforts |
To address this issue:
- Provide leadership training on the importance of safety leadership
- Include safety performance in management evaluations
- Encourage peer-to-peer accountability at all levels
- Celebrate leaders who consistently demonstrate safe behaviors
Without consistent consequences for safety violations, employees may perceive safety rules as optional or unimportant. This perception can lead to a gradual erosion of safety standards and increased risk of incidents.
To establish effective consequences:
- Develop a clear, graduated system of disciplinary actions
- Communicate the consequences of violations to all employees
- Apply consequences fairly and consistently across the organization
- Document all violations and actions taken
Also inconsistent disciplinary actions for similar safety violations can create a sense of unfairness and favoritism. This inconsistency can lead to resentment, decreased morale, and reduced compliance with safety rules.
To ensure consistent disciplinary actions:
- Create a standardized disciplinary matrix for safety violations
- Train supervisors on proper application of disciplinary measures
- Regularly review disciplinary actions for consistency
- Address any discrepancies or perceived unfairness promptly
By addressing these four aspects of inconsistent enforcement, organizations can significantly improve their BBS implementation and create a stronger safety culture.
5. Neglecting to Update Risk Assessments
Neglecting to update risk assessments can lead to serious safety oversights. One common mistake is relying on outdated hazard identification methods. As workplaces evolve, new risks emerge, making it crucial to regularly review and update your hazard identification processes.
Consider the following table comparing traditional and modern hazard identification methods:
Traditional Methods | Modern Methods |
Manual checklists | Digital safety apps |
Annual inspections | Continuous monitoring |
Generic assessments | Industry-specific tools |
Limited employee input | Crowdsourced reporting |
To avoid this mistake, implement a dynamic hazard identification system that:
- Utilizes advanced technology for real-time monitoring
- Encourages employee participation in reporting potential hazards
- Incorporates data analytics to identify trends and patterns
- Regularly updates assessment criteria based on industry best practices
Workplace changes, whether minor or significant, can introduce new risks or alter existing ones. Failing to reassess safety measures after such changes is a critical error in behaviour based safety (BBS) implementation.
Key instances requiring reassessment include:
- Introduction of new equipment or processes
- Changes in workplace layout or design
- Shifts in employee roles or responsibilities
- Modifications to work schedules or shift patterns
Safety standards are constantly evolving, reflecting advancements in research, technology, and best practices. Ignoring these updates can leave your workplace vulnerable to emerging risks and potentially non-compliant with regulatory requirements.
To stay current:
- Subscribe to industry publications and regulatory updates
- Attend safety conferences and workshops
- Participate in professional safety organizations
- Regularly review and update your BBS audit checklist
By addressing these common mistakes in risk assessment, you can significantly enhance your behaviour-based safety program and create a more robust safety culture in your organization.
6.Focusing Solely on Lagging Indicators
Many organizations fall into the trap of focusing solely on lagging indicators, particularly injury rates, when assessing their safety performance. While these metrics are important, they only tell part of the story and can lead to a reactive approach to safety management.
Lagging Indicators | Leading Indicators |
Injury rates | Near-miss reports |
Lost time incidents | Safety training completion |
Workers’ compensation costs | Safety observation frequency |
Overemphasizing injury rates can create a false sense of security when numbers are low, potentially masking underlying safety issues that haven’t yet resulted in injuries.
Leading indicators are proactive measures that can help predict and prevent future incidents. By neglecting these, companies miss out on valuable insights that could drive safety improvements.
Key leading indicators to consider:
- Employee participation in safety meetings
- Percentage of completed safety inspections
- Number of hazards identified and corrected
- Time taken to address safety concerns
Proactive safety efforts are crucial for a robust behaviour based safety (BBS) program. However, many organizations fail to measure and recognize these initiatives effectively.
Examples of proactive safety efforts to measure:
- Implementation of safety suggestions
- Engagement in safety committees
- Peer-to-peer safety observations
- Participation in voluntary safety training
By balancing both lagging and leading indicators and measuring proactive safety efforts, organizations can create a more comprehensive and effective BBS program. This approach not only helps prevent incidents but also fosters a culture of continuous safety improvement.
7.Lack of Employee Involvement in Safety Initiatives
A top-down safety management approach can significantly hinder employee involvement in safety initiatives. This traditional method often fails to tap into the valuable insights and experiences of frontline workers. Instead of fostering a culture of shared responsibility, it creates a disconnect between management and employees.
One of the most critical mistakes in behaviour based safety is overlooking the input of those who are closest to the daily operations. Workers often have unique perspectives on potential hazards and practical solutions.
Benefits of Worker Feedback | Consequences of Ignoring Feedback |
Improved hazard identification | Missed safety opportunities |
Practical, cost-effective solutions | Decreased employee morale |
Enhanced safety culture | Increased risk of incidents |
Higher employee engagement | Reduced trust in management |
Safety committees play a crucial role in bridging the gap between management and employees. Absence of safety committees can lead to:
- Lack of diverse perspectives in safety planning
- Reduced accountability for safety initiatives
- Missed opportunities for cross-departmental collaboration
- Decreased employee buy-in for safety programs
Failure to empower employees in decision-making can lead to:
- Delayed response to immediate safety concerns
- Reduced sense of ownership in safety outcomes
- Decreased motivation to actively participate in safety initiatives
- Missed opportunities for innovative safety solutions
By addressing these issues, organizations can create a more inclusive and effective behaviour based safety program, leading to improved safety outcomes and a stronger safety culture.
Avoiding these seven common behavior based safety mistakes is crucial for creating a robust safety culture in any organization. By addressing near misses, providing comprehensive employee training, effectively communicating safety policies, consistently enforcing rules, regularly updating risk assessments, balancing leading and lagging indicators, and actively involving employees in safety initiatives, companies can significantly reduce workplace accidents and injuries.
Remember, a successful behavior based safety program requires continuous effort, commitment from all levels of the organization, and a willingness to adapt to changing circumstances. By prioritizing these areas and fostering a proactive approach to safety, you can create a safer work environment and protect your most valuable asset – your employees. Take action today to review your current safety practices and implement necessary improvements to ensure a safer tomorrow.